Destylacja rozpuszczalników to proces, który polega na oddzieleniu składników mieszaniny na podstawie różnicy ich temperatur wrzenia. Jest to technika szeroko stosowana w chemii, przemyśle farmaceutycznym oraz w produkcji różnych substancji chemicznych. Proces ten zaczyna się od podgrzewania cieczy, co powoduje jej parowanie. W wyniku tego pary unoszą się do góry, a następnie skraplają się w chłodniejszej części aparatu destylacyjnego. Zbierane są w postaci cieczy, zwanej destylatem. Kluczowym elementem tego procesu jest to, że różne substancje mają różne temperatury wrzenia, co umożliwia ich skuteczne oddzielanie. Na przykład, w przypadku destylacji wody i alkoholu etylowego, alkohol odparowuje w niższej temperaturze niż woda, co pozwala na jego oddzielenie. Destylacja rozpuszczalników jest nie tylko efektywna, ale także ekologiczna, ponieważ pozwala na odzyskiwanie substancji chemicznych z odpadów oraz ich ponowne wykorzystanie.
Jakie są rodzaje destylacji rozpuszczalników i ich zastosowania
Wyróżniamy kilka rodzajów destylacji rozpuszczalników, które różnią się między sobą metodą przeprowadzania procesu oraz zastosowaniem. Najpopularniejsze z nich to destylacja prosta, frakcyjna oraz próżniowa. Destylacja prosta jest najczęściej stosowana do separacji substancji o znacznej różnicy temperatur wrzenia. Umożliwia ona uzyskanie jednego produktu o wysokiej czystości. Z kolei destylacja frakcyjna jest bardziej skomplikowana i wykorzystywana jest do oddzielania mieszanin zbliżonych pod względem temperatur wrzenia. Dzięki zastosowaniu kolumny frakcyjnej możliwe jest wielokrotne skraplanie i odparowywanie substancji, co prowadzi do uzyskania wyższej czystości produktów końcowych. Destylacja próżniowa natomiast odbywa się w obniżonym ciśnieniu, co pozwala na destylację substancji o wysokiej temperaturze wrzenia bez ryzyka ich degradacji. Każda z tych metod ma swoje specyficzne zastosowania w różnych branżach, takich jak przemysł chemiczny, petrochemiczny czy farmaceutyczny.
Jakie są zalety i ograniczenia destylacji rozpuszczalników
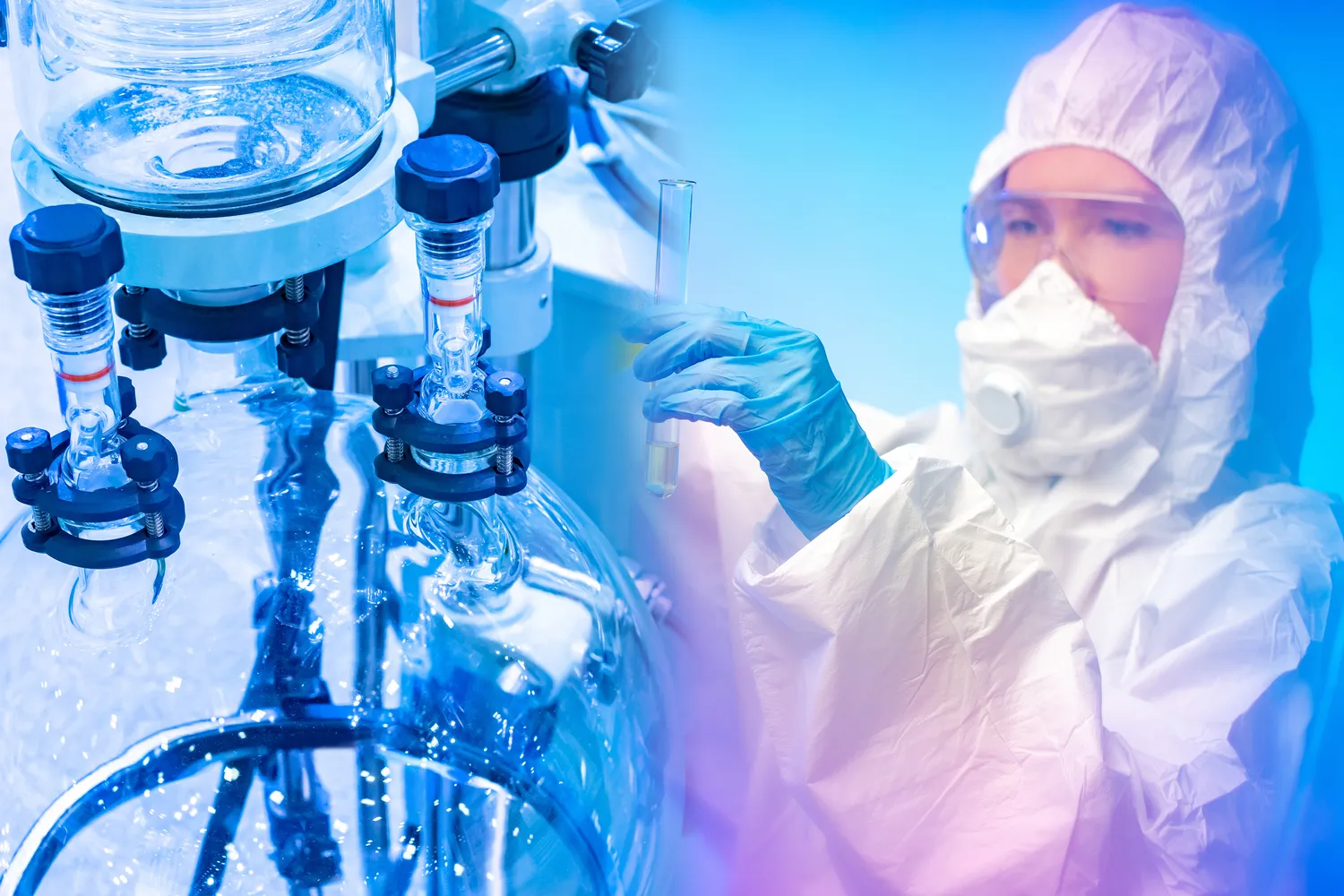
Destylacja rozpuszczalników ma wiele zalet, które sprawiają, że jest to jedna z najczęściej stosowanych metod separacji w przemyśle chemicznym i laboratoryjnym. Przede wszystkim pozwala na uzyskanie wysokiej czystości produktów końcowych dzięki selektywnemu oddzielaniu składników mieszaniny. Proces ten jest również stosunkowo prosty do przeprowadzenia i może być zautomatyzowany, co zwiększa efektywność produkcji. Dodatkowo destylacja umożliwia odzyskiwanie cennych surowców z odpadów, co przyczynia się do ochrony środowiska i zmniejszenia kosztów produkcji. Niemniej jednak istnieją również pewne ograniczenia związane z tym procesem. Przede wszystkim nie zawsze jest możliwe oddzielenie składników o bardzo zbliżonych temperaturach wrzenia, co może prowadzić do obniżonej efektywności separacji. Ponadto proces ten wymaga dużych nakładów energii, szczególnie w przypadku dużych instalacji przemysłowych. Warto również zauważyć, że niektóre substancje mogą ulegać degradacji podczas podgrzewania, co może wpływać na jakość końcowego produktu.
Jakie urządzenia są wykorzystywane w procesie destylacji rozpuszczalników
Aby przeprowadzić proces destylacji rozpuszczalników, konieczne jest użycie odpowiednich urządzeń, które umożliwiają efektywne oddzielanie składników mieszaniny. Podstawowym elementem każdego systemu destylacyjnego jest aparat destylacyjny, który może mieć różne formy w zależności od rodzaju przeprowadzanej destylacji. W przypadku destylacji prostej najczęściej stosuje się kolbę okrągłodenna oraz chłodnicę do kondensacji pary. W przypadku bardziej skomplikowanej destylacji frakcyjnej używa się kolumn frakcyjnych, które składają się z wielu poziomych sekcji umożliwiających wielokrotne skraplanie i odparowywanie składników mieszaniny. Dodatkowo istotnym elementem systemu są urządzenia kontrolujące temperaturę oraz ciśnienie wewnątrz aparatu destylacyjnego, co pozwala na precyzyjne zarządzanie procesem separacji. W nowoczesnych instalacjach przemysłowych często stosuje się automatyczne systemy sterowania oraz monitorowania procesu, co zwiększa efektywność i bezpieczeństwo pracy.
Jakie są zastosowania destylacji rozpuszczalników w przemyśle
Destylacja rozpuszczalników znajduje szerokie zastosowanie w różnych gałęziach przemysłu, co czyni ją kluczowym procesem technologicznym. W przemyśle chemicznym jest wykorzystywana do oczyszczania i separacji substancji chemicznych, takich jak alkohole, kwasy czy zasady. Dzięki temu możliwe jest uzyskanie wysokiej czystości reagentów, które są niezbędne do produkcji różnych związków chemicznych. W przemyśle farmaceutycznym destylacja odgrywa istotną rolę w produkcji leków, gdzie czystość substancji czynnych ma kluczowe znaczenie dla ich skuteczności i bezpieczeństwa stosowania. Proces ten pozwala również na odzyskiwanie rozpuszczalników organicznych, co przyczynia się do zmniejszenia kosztów produkcji oraz minimalizacji wpływu na środowisko. W branży petrochemicznej destylacja jest podstawową metodą separacji frakcji ropy naftowej, co umożliwia uzyskanie paliw oraz innych produktów chemicznych. Destylacja rozpuszczalników znajduje także zastosowanie w przemyśle spożywczym, gdzie wykorzystywana jest do ekstrakcji aromatów oraz konserwantów z surowców naturalnych.
Jakie są nowoczesne technologie w destylacji rozpuszczalników
W ostatnich latach nastąpił znaczny rozwój technologii związanych z destylacją rozpuszczalników, co przyczyniło się do zwiększenia efektywności tego procesu oraz poprawy jakości uzyskiwanych produktów. Jednym z najważniejszych trendów jest automatyzacja procesów destylacyjnych, która pozwala na precyzyjne kontrolowanie parametrów pracy aparatury oraz monitorowanie jakości produktów w czasie rzeczywistym. Nowoczesne systemy sterowania opierają się na zaawansowanych algorytmach, które umożliwiają optymalizację pracy urządzeń oraz minimalizację zużycia energii. Kolejnym innowacyjnym rozwiązaniem są kolumny destylacyjne o wysokiej wydajności, które charakteryzują się większą powierzchnią wymiany masy oraz lepszymi właściwościami separacyjnymi. Dzięki temu możliwe jest osiągnięcie wyższej czystości produktów końcowych przy niższym zużyciu energii. Warto również wspomnieć o technologii membranowej, która staje się coraz bardziej popularna jako alternatywa dla tradycyjnej destylacji. Proces ten polega na wykorzystaniu membran selektywnych do separacji składników mieszaniny bez konieczności podgrzewania, co znacząco obniża koszty energetyczne i wpływ na środowisko.
Jakie są wyzwania związane z destylacją rozpuszczalników
Mimo licznych zalet i szerokiego zastosowania, proces destylacji rozpuszczalników wiąże się z pewnymi wyzwaniami, które mogą wpływać na jego efektywność oraz bezpieczeństwo. Jednym z głównych problemów jest konieczność precyzyjnego zarządzania temperaturą i ciśnieniem w aparatach destylacyjnych. Niewłaściwe ustawienia mogą prowadzić do obniżenia jakości uzyskiwanych produktów lub nawet do ich degradacji. Ponadto wiele substancji chemicznych może być toksycznych lub łatwopalnych, co stwarza dodatkowe ryzyko podczas przeprowadzania procesu destylacji. W związku z tym konieczne jest wdrażanie odpowiednich procedur bezpieczeństwa oraz stosowanie nowoczesnych technologii monitorowania i kontroli procesów. Kolejnym wyzwaniem jest kwestia ochrony środowiska, ponieważ wiele tradycyjnych metod destylacyjnych generuje znaczne ilości odpadów oraz emisji gazów cieplarnianych. Dlatego coraz większy nacisk kładzie się na rozwój bardziej ekologicznych technologii, które minimalizują negatywny wpływ na otoczenie.
Jakie są przyszłe kierunki rozwoju destylacji rozpuszczalników
Przyszłość destylacji rozpuszczalników będzie prawdopodobnie związana z dalszym rozwojem technologii oraz innowacyjnymi podejściami do tego procesu. W miarę jak rośnie zapotrzebowanie na czyste i ekologiczne metody produkcji chemikaliów, można spodziewać się wzrostu zainteresowania technologiami niskotemperaturowymi oraz membranowymi jako alternatywami dla tradycyjnej destylacji. Dodatkowo rozwój sztucznej inteligencji i uczenia maszynowego może przyczynić się do optymalizacji procesów destylacyjnych poprzez analizę danych operacyjnych i prognozowanie wydajności produkcji. Warto również zwrócić uwagę na rosnącą rolę recyklingu i odzysku surowców w kontekście zrównoważonego rozwoju przemysłu chemicznego. Destylacja może odegrać kluczową rolę w tych procesach, umożliwiając skuteczne oddzielanie cennych substancji z odpadów przemysłowych czy zużytych produktów chemicznych. Współpraca między naukowcami a przemysłem będzie miała istotne znaczenie dla opracowywania nowych metod i technologii, które będą bardziej efektywne i przyjazne dla środowiska.
Jakie są przykłady zastosowań destylacji rozpuszczalników w laboratoriach
W laboratoriach chemicznych destylacja rozpuszczalników jest powszechnie stosowana jako jedna z podstawowych metod oczyszczania substancji chemicznych oraz przygotowywania prób do dalszych badań. Przykładem może być oczyszczanie alkoholu etylowego poprzez destylację prostą lub frakcyjną, co pozwala na uzyskanie wysokiej czystości reagentu niezbędnego w syntezach chemicznych czy analizach laboratoryjnych. Innym zastosowaniem jest izolacja olejków eterycznych z roślin za pomocą destylacji parowej, co umożliwia pozyskiwanie cennych substancji aromatycznych wykorzystywanych w przemyśle kosmetycznym czy spożywczym. Laboratoria analityczne często korzystają z technik destylacyjnych do przygotowywania próbek do analizy chromatograficznej czy spektroskopowej, gdzie czystość składników ma kluczowe znaczenie dla uzyskania wiarygodnych wyników badań. Destylacja znajduje również zastosowanie w badaniach nad nowymi materiałami chemicznymi, gdzie może być wykorzystywana do oceny właściwości fizykochemicznych różnych substancji poprzez ich separację i oczyszczanie przed dalszymi badaniami.
Jakie są różnice między tradycyjną a nowoczesną destylacją rozpuszczalników
Różnice między tradycyjną a nowoczesną destylacją rozpuszczalników dotyczą przede wszystkim technologii wykorzystywanych do przeprowadzania tego procesu oraz efektywności energetycznej poszczególnych metod. Tradycyjna destylacja opiera się głównie na prostych aparatach takich jak kolby okrągłodenna czy chłodnice, które wymagają dużej ilości energii cieplnej do podgrzewania cieczy i skraplania pary. Nowoczesne technologie natomiast wykorzystują zaawansowane systemy automatyzacji oraz kontrolowania parametrów procesu, co pozwala na optymalizację pracy urządzeń i minimalizację zużycia energii. Ponadto nowoczesna destylacja często korzysta z innowacyjnych materiałów konstrukcyjnych oraz technologii membranowych, które umożliwiają separację składników bez konieczności podgrzewania ich do wysokich temperatur.