Robotyzacja procesów spawalniczych to temat, który zyskuje na znaczeniu w dzisiejszym przemyśle. Wprowadzenie robotów do procesów spawania ma na celu zwiększenie wydajności, precyzji oraz bezpieczeństwa pracy. Tradycyjne metody spawania często wiążą się z dużym ryzykiem dla pracowników, a także z koniecznością posiadania wysokich umiejętności manualnych. Roboty, które wykonują te zadania, eliminują wiele zagrożeń związanych z pracą w trudnych warunkach. Dzięki zastosowaniu nowoczesnych technologii, takich jak sztuczna inteligencja i uczenie maszynowe, roboty są w stanie dostosować swoje działania do zmieniających się warunków produkcji. W efekcie możliwe jest osiągnięcie znacznie wyższej jakości spawów oraz redukcja odpadów materiałowych. Warto również zauważyć, że robotyzacja procesów spawalniczych przyczynia się do obniżenia kosztów produkcji, co jest niezwykle istotne w konkurencyjnym środowisku rynkowym.
Jakie są zalety i wady robotyzacji spawania
Robotyzacja procesów spawalniczych niesie ze sobą szereg zalet, ale także pewne wyzwania, które należy rozważyć przed podjęciem decyzji o wdrożeniu tej technologii. Do najważniejszych zalet należy zwiększenie efektywności produkcji dzięki możliwości pracy robotów przez całą dobę bez przerw. Roboty spawalnicze charakteryzują się również dużą precyzją, co przekłada się na wyższą jakość wykonywanych spawów. Dodatkowo, automatyzacja procesów pozwala na zmniejszenie liczby błędów ludzkich, co jest kluczowe w branżach wymagających wysokiej dokładności. Z drugiej strony, wdrożenie robotyzacji wiąże się z wysokimi kosztami początkowymi oraz koniecznością przeszkolenia personelu do obsługi nowych urządzeń. Istnieje także ryzyko utraty miejsc pracy dla pracowników zajmujących się tradycyjnym spawaniem, co może budzić kontrowersje społeczne.
Jakie technologie są wykorzystywane w robotyzacji spawania
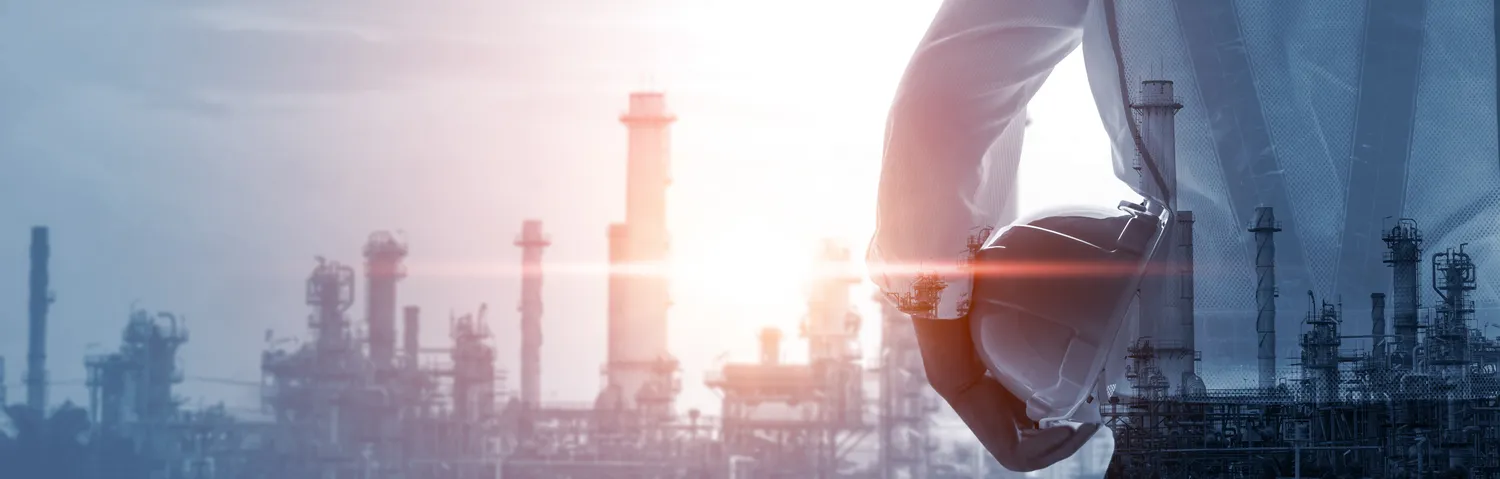
W kontekście robotyzacji procesów spawalniczych stosuje się różnorodne technologie, które mają na celu zwiększenie efektywności i jakości wykonywanych prac. Jednym z najpopularniejszych rozwiązań jest wykorzystanie robotów przemysłowych wyposażonych w zaawansowane systemy sterowania oraz sensory. Dzięki nim roboty mogą precyzyjnie monitorować parametry procesu spawania i dostosowywać swoje działania do aktualnych warunków. Współczesne systemy spawalnicze często korzystają z technologii MIG/MAG oraz TIG, które umożliwiają uzyskanie wysokiej jakości połączeń metalowych. Dodatkowo, coraz częściej stosuje się technologie laserowe oraz plazmowe, które pozwalają na szybkie i dokładne cięcie oraz spawanie materiałów o różnych grubościach. Integracja robotów z systemami CAD/CAM umożliwia automatyczne generowanie programów spawania na podstawie projektów 3D, co znacznie przyspiesza proces produkcji.
Jakie są przyszłe kierunki rozwoju robotyzacji w spawalnictwie
Przyszłość robotyzacji procesów spawalniczych wydaje się być obiecująca i pełna innowacji. W miarę jak technologia rozwija się w szybkim tempie, można spodziewać się coraz większej automatyzacji procesów produkcyjnych. Jednym z kluczowych kierunków rozwoju będzie integracja robotyzacji z Internetem Rzeczy (IoT), co pozwoli na zbieranie danych w czasie rzeczywistym oraz ich analizę w celu optymalizacji procesów produkcyjnych. Wprowadzenie bardziej zaawansowanych algorytmów uczenia maszynowego umożliwi robotom samodzielne uczenie się na podstawie doświadczeń zdobytych podczas pracy, co przyczyni się do dalszego zwiększenia efektywności i jakości spawania. Ponadto rozwój technologii współpracy między ludźmi a robotami (coboty) otworzy nowe możliwości w zakresie elastyczności produkcji oraz dostosowywania się do zmieniających się potrzeb rynku. Można również przewidywać większą dostępność rozwiązań mobilnych, które umożliwią wykonywanie prac spawalniczych w różnych lokalizacjach bez potrzeby transportu ciężkiego sprzętu.
Jakie są najczęstsze zastosowania robotyzacji w spawalnictwie
Robotyzacja procesów spawalniczych znajduje zastosowanie w wielu branżach, co czyni ją niezwykle wszechstronnym rozwiązaniem. Jednym z najczęściej spotykanych obszarów wykorzystania robotów spawalniczych jest przemysł motoryzacyjny, gdzie automatyzacja pozwala na szybkie i precyzyjne łączenie elementów karoserii. W tym sektorze, gdzie produkcja musi być nieprzerwana i efektywna, roboty spawalnicze odgrywają kluczową rolę w zapewnieniu wysokiej jakości oraz powtarzalności procesów. Kolejnym istotnym zastosowaniem jest przemysł stoczniowy, gdzie roboty wykonują skomplikowane spawy na dużych konstrukcjach, takich jak kadłuby statków. Dzięki zastosowaniu technologii robotyzacji możliwe jest osiągnięcie znacznie lepszej jakości spawów oraz redukcja czasu potrzebnego na wykonanie poszczególnych operacji. W branży budowlanej roboty spawalnicze są wykorzystywane do łączenia stalowych elementów konstrukcyjnych, co przyspiesza proces budowy i zwiększa bezpieczeństwo pracy. Warto również zauważyć, że robotyzacja znajduje zastosowanie w produkcji sprzętu AGD oraz elektroniki, gdzie precyzyjne połączenia są kluczowe dla funkcjonalności produktów.
Jakie umiejętności są potrzebne do pracy z robotami spawalniczymi
Praca z robotami spawalniczymi wymaga od pracowników posiadania specyficznych umiejętności oraz wiedzy technicznej. Kluczowym aspektem jest znajomość programowania robotów, co pozwala na dostosowanie ich działania do konkretnych potrzeb produkcji. Osoby zajmujące się obsługą robotów muszą być zaznajomione z różnymi językami programowania oraz systemami sterowania, które są wykorzystywane w automatyzacji procesów spawalniczych. Dodatkowo ważne jest zrozumienie zasad działania technologii spawalniczych, takich jak MIG/MAG czy TIG, aby móc skutecznie monitorować jakość wykonywanych spawów. Umiejętność analizy danych oraz rozwiązywania problemów technicznych jest również istotna, ponieważ często pojawiają się sytuacje wymagające szybkiego reagowania na awarie lub nieprawidłowości w procesie produkcji. W związku z dynamicznym rozwojem technologii, pracownicy powinni regularnie uczestniczyć w szkoleniach i kursach doskonalących swoje umiejętności.
Jakie wyzwania stoją przed firmami wdrażającymi robotyzację
Wdrażanie robotyzacji procesów spawalniczych wiąże się z szeregiem wyzwań, które firmy muszą pokonać, aby skutecznie zintegrować nowe technologie w swoich zakładach. Jednym z głównych problemów są wysokie koszty początkowe związane z zakupem sprzętu oraz oprogramowania. Firmy często muszą inwestować znaczne sumy pieniędzy na etapie wdrożenia, co może być barierą dla mniejszych przedsiębiorstw. Kolejnym wyzwaniem jest konieczność przeszkolenia pracowników do obsługi nowych systemów oraz technologii. Wiele osób obawia się utraty pracy na rzecz automatów, co może prowadzić do oporu przed zmianami w organizacji. Ponadto integracja nowych rozwiązań z istniejącymi systemami produkcyjnymi może być skomplikowana i czasochłonna. Firmy muszą także zmierzyć się z kwestią utrzymania sprzętu oraz zapewnienia odpowiednich warunków do jego pracy, co wiąże się z dodatkowymi kosztami operacyjnymi.
Jakie są przykłady firm wykorzystujących robotyzację w spawaniu
Na rynku istnieje wiele firm, które skutecznie wdrożyły robotyzację procesów spawalniczych i osiągnęły znaczące korzyści dzięki tej technologii. Przykładem może być koncern motoryzacyjny Toyota, który od lat stosuje zaawansowane systemy automatyzacji w swoich zakładach produkcyjnych. Roboty spawalnicze w fabrykach Toyoty przyczyniają się do zwiększenia wydajności oraz poprawy jakości produkowanych pojazdów. Innym przykładem jest firma Boeing, która wykorzystuje roboty do spawania elementów kadłubów samolotów. Dzięki automatyzacji możliwe jest osiągnięcie wysokiej precyzji oraz redukcja czasu potrzebnego na wykonanie skomplikowanych połączeń metalowych. W Europie wiele firm zajmujących się produkcją sprzętu AGD również korzysta z technologii robotycznych w procesach spawania, co pozwala im na utrzymanie konkurencyjności na rynku globalnym. Przykładem takiej firmy jest Bosch, która inwestuje w nowoczesne linie produkcyjne wyposażone w robota spawalniczego do łączenia komponentów urządzeń kuchennych.
Jakie są trendy w rozwoju robotyzacji procesów spawalniczych
Rozwój technologii związanych z robotyzacją procesów spawalniczych podlega dynamicznym zmianom i ewolucji w odpowiedzi na potrzeby rynku oraz postęp technologiczny. Jednym z najważniejszych trendów jest rosnąca integracja sztucznej inteligencji i uczenia maszynowego w systemach automatyzacji. Dzięki tym technologiom roboty będą mogły samodzielnie uczyć się na podstawie doświadczeń zdobytych podczas pracy oraz optymalizować swoje działania w czasie rzeczywistym. Kolejnym istotnym kierunkiem rozwoju jest miniaturyzacja urządzeń oraz ich mobilność, co umożliwi łatwiejsze dostosowanie systemów do różnych warunków pracy i lokalizacji produkcji. Coraz większą uwagę zwraca się także na kwestie związane z ekologią i efektywnością energetyczną procesów produkcyjnych, co prowadzi do poszukiwania rozwiązań zmniejszających zużycie energii przez maszyny oraz ograniczających emisję szkodliwych substancji do atmosfery. Wzrasta również znaczenie współpracy między ludźmi a robotami (coboty), co pozwala na elastyczne dostosowywanie się do zmieniających się potrzeb produkcji bez konieczności całkowitej automatyzacji procesu.
Jakie są perspektywy dla przyszłości robotyzacji procesów spawania
Perspektywy dla przyszłości robotyzacji procesów spawania wyglądają bardzo obiecująco i wskazują na dalszy rozwój tej technologii w różnych branżach przemysłowych. Zwiększone zainteresowanie automatyzacją wynika przede wszystkim z potrzeby poprawy wydajności produkcji oraz jakości produktów końcowych. W miarę jak technologia staje się coraz bardziej dostępna i przystępna cenowo dla różnych przedsiębiorstw, można spodziewać się wzrostu liczby firm decydujących się na wdrożenie rozwiązań opartych na robotyzacji. Również rozwój technologii komunikacyjnych sprawia, że integracja systemów automatycznych staje się łatwiejsza niż kiedykolwiek wcześniej. Możliwości analizy danych zbieranych przez maszyny otwierają nowe horyzonty dla optymalizacji procesów produkcyjnych oraz przewidywania awarii czy problemów związanych z jakością produktów. Zmiany te mogą prowadzić do jeszcze większej elastyczności produkcji oraz szybszego dostosowywania się do zmieniających się potrzeb rynku.